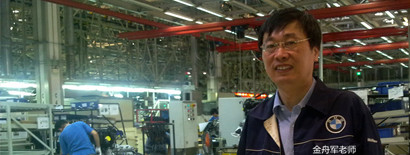
谢宁DOE培训公开课咨询课程—欢迎企业培训公开课和机构合作垂询
谢宁DOE培训公开课-培训地点:江苏无锡万达广场 每月开班 小班教学、满四人开班
金舟军老师 手机/微信:13816949004 QQ邮箱:923503608@qq.com
以应用为导向的谢宁DOE培训,学员培训后就会应用谢宁DOE,金舟军老师通过严格的培训流程确保顾客满意
请点击查看—金舟军质量管理工具培训咨询实施流程
谢宁DOE培训讲师质量专家金舟军,谢宁DOE培训咨询机构上海科租企业管理咨询有限公司主办,是专业、实战、解决问题的培训
请点击查看—金舟军质量管理工具培训咨询实施流程
谢宁DOE培训讲师质量专家金舟军,谢宁DOE培训咨询机构上海科租企业管理咨询有限公司主办,是专业、实战、解决问题的培训
最有价值的谢宁DOE培训公司
上海科租企业管理咨询有限公司金舟军老师自办谢宁DOE培训咨询公司,培训老师自办公司省出了业务费用和老板利润,客户的培训费全部变为培训老师的培训费,能为客户提供优质服务,客户培训价值最大化值 。只要学员参加过质量培训咨询课程,将为学员提供终生的培训课程答疑。
最具专业的谢宁DOE培训讲师
金舟军二十多年专业从事谢宁DOE培训讲师,专业涉及质量管理和精益生产课程,客户涉及世界五百强企业, 每个培训项目的客户都有培训现场的视频和照片为证。金舟军老师课程以应用为导向,课堂上只讲干货,绝不以无关的游戏打发时间。
培训的客户-全部有客户培训现场照片、视频为证!


重庆长安汽车、上海延锋韦世通、上海NEC、上海德尔福、武汉东风汽车、江苏东风起亚、江苏麦格纳、安徽康佳电器、、安徽博西华、上海奥托立夫、浙江海信惠尔浦、沈阳宝马汽车、上海大金空调、辽宁大连固特异轮胎、长春大众集团、湖北武汉佛吉亚、上汽集团、吉林一汽集团、广西上汽通用五菱、广西玉林重工、江西长力股份 北京北汽福田、深圳中兴通迅、福建新能源科技、湖南三一重工、苏州恩斯克轴承、河北天威光伏、武汉哈金森、苏州力特奥维斯、重庆 嘉陵集团 福建奔驰汽车、辽宁大连大众变速箱 广东广州京信通信、深圳中兴通讯 河南利达光电 河南新乡豫新 河北莱尼、山东莱尼 、山东胜地、陕西中航、湖南时代电气、天津中核
谢宁DOE培训课程公开课视频--点击图片即观看好看视频金舟军老师好看视频主页
金舟军老师谢宁DOE培训优势谢宁DOE培训课程公开课视频--点击图片即观看好看视频金舟军老师好看视频主页
结合客户案例的实战型培训 包括后服务答疑的全过程
金舟军老师通过五大步骤结合客户案例讲解,确保学员学完全就会在工作中应用: 1 .案例网络调研、2.案例学员预习、3. 现场案例调研、4.案例练习点评、5.售后案例答疑。
1.案例网络调研
培训意向一经确定,金舟军老师就要与客户进行网络沟通,确定谢宁DOE实施难点,收集谢宁DOE实施资料,并就实施资料的细节进行沟通,并了解客户学习谢宁DOE的目的。
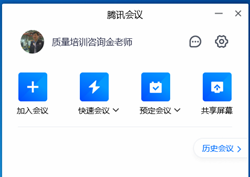
2.学员案例预习
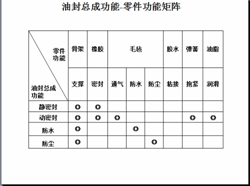
3. 现场案例调研
金舟军老师根据谢宁DOE实施中的难点,事先为学员出谢宁DOE的预习题,帮助学员提前思考怎样解决实施案例的难点,同时也预习课堂讲解的知识。
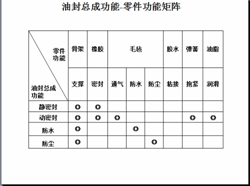
3. 现场案例调研
培训前一天,金舟军老师会到客户现场进行一天的现场调研,查找客户谢宁DOE实施V情况,并为课堂针对客户实施谢宁DOE中的问题讲解做准备。
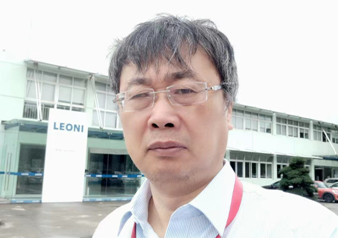
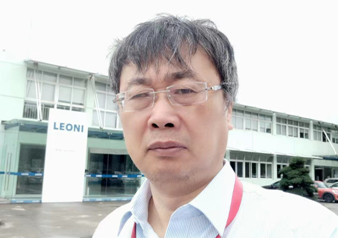
4.案例练习点评
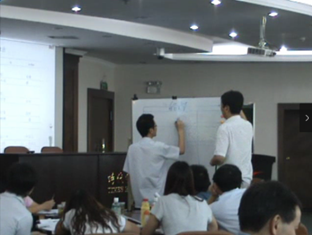
5.售后案例答疑
培训完成后一年之内,如果客户在实施谢宁DOE过程中有什么问题,可以为客户组织腾讯会议的在线答疑至少三次。
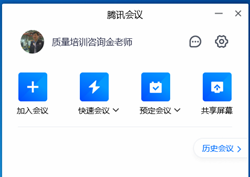
根据案例实施中的难点问题,每天培训约有五十分钟的客户案例分组练习,每组学员的案例练习金舟军老师都要做详细的点评,确保学员学完全就会在工作中应用。
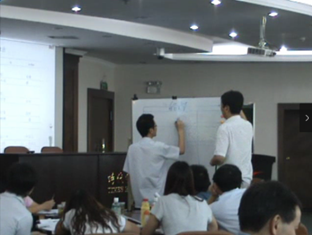
5.售后案例答疑
培训完成后一年之内,如果客户在实施谢宁DOE过程中有什么问题,可以为客户组织腾讯会议的在线答疑至少三次。
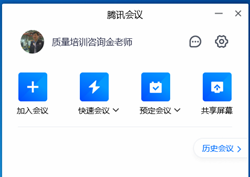
< 谢宁DOE培训课程(夏宁DOE培训)介绍
谢宁系统SS(谢宁方法)是由道林•谢宁(DorianShainin)研究开发的解决产品设计开发、过程设计开发和制造过程控制中的质量问题的系统方法和工具。工具名称作为服务商标受法律保护,很少文章讨论,而公众不知详细内容,从SPC、DOE、数理统计和部件交换技求导出,用现成公式,而不需数理统计知识和计算,谢宁(Shainin)DOE工具作为一个由果到因系统解决问题的方法,采用从果到因的方式,以现有结果为起点,反向开展搜索根本原因。
谢宁(Shainin)DO解决问题针对性强、不打断生产、效果好的优点。“没有戴明,美国就不会有质量哲学;没有朱兰,美国就不会有质量的方向;没有谢宁,美国就无从解决质量问题”。这句名言总结了美国最伟大的三位质量大师的贡献。
由于谢宁系统SS工具名称作为服务商标受法律保护,美国很少文章讨论,而公众不知详细内容,在美国谢宁系统SS的培训美国谢宁独家经营。目前国内的谢宁DOE培训如果是源自这本博特著、遇今译的《世界级质量管理工具DOE》(中文版),这点可以课程大纲与该书目录一致看出,英文版的有心之错和中文版翻译无心之错都被继承。
质量培训专家金舟军研究应用谢宁系统SS近十年,多方收集道林•谢宁及世界同行之成果,在培训咨询颇有心得,一些原始案例主要是针对产品设计问题的,然而国内厂家更加关注工艺过程质量问题,金舟军的培训也关注工艺过程质量问题方面的应用,更涉及到电子、机械、化工等制造行业的产品设计问题和工艺过程质量问题。
谢宁DOE培训
培训课程大纲
一.培训目的:通过本课程的学习,使学员能掌握谢宁(Shainin)DOE工具解决工艺过程质量问题。
二.培训对象:产品设计开发人员、工艺设计开发人员、质量人员、管理质量工程师和现场工程师。
三.培训课程内容
1.谢宁系统ShaininSystem简介 金舟军原创抄袭必告
道林•谢宁DorianShainin简介
SS商标或服务商标
案例讨论-谢宁系统七种工具能独立运用吗
2.谢宁系统主要特点
谢宁系统解决问题类型
解决问题存在的误区
案例讨论-PPAP提交不满要求能用谢宁系统吗
3.确定改进项目
改进项目金舟军原创抄袭必告
征状问题原因
案例讨论-怎样将征状分解成问题
4.问题绿Y的确定
事件次数-特性值
应力极限转换
能量工具解决技术问题
项目定义树
案例讨论-怎样开展应力极限转换
5.测量系统分析-Isoplot图
测量系统的变差类型
Isoplot作图方法
Isoplot接受准则B
案例讨论-怎样开展应力极限转换
6.红X、粉红X和浅粉红X
产品设计和开发绿Y与红x
过程设计和开发绿Y与红x
红x影响平方和的平方根原理
案例讨论-平方根原理验证
7.RedX策略
策略图
问题解决树
找球游戏启示
基于事实结果反向搜索
案例讨论-完成一个问题解决树
8.搜索根本原因三步法
可能原因
最有可能原因金舟军原创抄袭必告
根本原因
案例讨论-完成一个最有可能原因分析
9.变差族分析
多层变差图在RedX策略的位置
多层变差图Multi-VariChart
多层变差模型
分层法调查表
多层变差图
变差过程分析案例
集中图案例
策略图案例
案例讨论-用集中图分析一个案例
10.部件搜索ComponentSearch
部件搜索在RedX策略的位置
部件搜索统计学原理
双样本t检验
显著性检验 金舟军原创抄袭必告
好的BOB和坏的WOW部件选取
谢宁DOE杠杆leveraging作用
产品的功能框图
部件搜索分析流程和案例
第1阶段球场
第2阶段排除
第3阶段诱骗实验
第4阶段分析
部件搜索在汽车零件售后市场质量分析应用
计时器部件搜索案例
案例讨论-怎样选取好的BOB和坏的WOW部件
11.部件成对比较PairedComparisons
部件成对比较在RedX策略的位置
部件成对比较统计学原理
图基检验TukeyTest
图基检验的统计学金原理-假设性检验
部件质量特性搜索 金舟军原创抄袭必告
好的BOB和坏的WOW部件选取
杠杆作用leveraging利用BOB与WOW差异
产品功能与产品特性因果图
成对比较分析流程和案例
成对比较在汽车零件关键、特殊特性识别中的应用
马达噪音的实验设计研究
案例讨论-怎样选取好的BOB和坏的WOW部件
12.部件成组比较GroupComparisons
部件成组比较在RedX策略的位置
成组比较分析流程和案例
推力式柱塞密封案例
案例讨论-部件成组与成对比较有什么不同
13.产品/过程的搜索ProcessSearch
产品/过程的搜索在RedX策略的位置
变差族显示变化是时间性
好的和坏的过程选取
因果图、KCC&KPC矩阵
产品/过程的搜索分析流程和案例
产品/过程的搜索在汽车零件关键、特殊特性识别中的应用
注塑超出20%的废品率案例
案例讨论-过程的搜索优化某制造过程
14.变量搜索技术VariablesSearch
变量搜索在RedX策略的位置
变量和水平的确定
显著性检验
变量搜索的确定工艺参数
变量搜索的分析流程和案例
第1阶段球场 金舟军原创抄袭必告
第2阶段排除
第3阶段诱骗实验
第4阶段分析
产品/过程的搜索在零件工艺参数特殊特性识别中的应用
案例讨论-变量搜索筛选某制造过程参数
15.全因子实验FullFactorials
全因子实验在RedX策略的位置
什么是实验设计
因果关系与函数关系
编码值与真实值
一次一因子实验法
数理统计基础
总体分布统计量
正态分布的密度函数
正态分布概率
制造金弹簧实例
中心极限定理
单值比较&均值比较
全因子实验法
无交互作用的正交实验设计
有交互作用的正交实验设计
正交表性质
两水平全因子设计
全因子实验案例
全因子实验设计特点
部分因子实验设计
正交部分因子实验
实验设计要解决的问题
部分因子设计两种生成方法
案例讨论-针对四个因子全因子实验水平设置
16.改进的确认-B与C比较Bvs.C
Bvs.C在RedX策略的位置
改进目标的舟确定
B与C比较
B与C比较过程分析案例
案例讨论-针对一个改进结果做B与C比较
17.公差设计RealisticToleranceParallelogramplot
公差设计在RedX策略的位置
过程工艺参数优化设计和目标值
同步工程
制造过程能力和测量过程能力分析
回归分析确定过程工艺参数上下公差
工艺参数优化设计和目标值案例
案例讨论-针对一个改进结果做B与C比较
18.响应曲面DOE简介
调优运算EVOP简介
案例讨论-调优运算缺点是什么
19.预控图
预控图在RedX策略的位置
预控图与控制图 金舟军原创抄袭必告
预控图实施流程
预控图应用案例
案例讨论-怎样应用预控图军作业准备验证
20.谢宁DOE开展的流程
判断的方法是否可以解决的具体问题
问题的特征值是否可测量
减少搜索范围
确定根本因子
量化因子的效应
验证改进的建议
确定工艺参数边界
控制过程
四.谢宁DOE培训课程学时每天6.5小时,共三-四天
汽车制造企业应用谢宁DOE介绍
ISO/TS16949对谢宁DOE应用要求
ISO/TS16949:2009版
8.1.1统计工具的确定
在质量先期策划中必须确定每一过程适用的统计工具,并包括在控制计划中。
ISO/TS16949:2002版指南
8.1.1统计工具的确定
应用包括:
。用于产品开发的统计方法,例如:变差分析,回归分析,可靠度分析和预测
。用于所采购产品的分析方法,例如:直方图和阶层图,柏拉图故障分析,抽样计划,接受统计的准则
。用于产品特性和过程参数经常性验证的统计方法,包括过程能力研究、控制图、柏拉图分析、变差分析(特殊原因、
普通原因)
。用于现场分析的统计方法,包括:可靠度评审、柏拉图分析、可追溯性分析和SHAININ技术
见顾客特殊要求手册。基于统计方法的测量系统分析
谢宁DOE在通用汽车 General Motors应用
Finding the Red X
Quality Drives Customer Enthusiasm
Statistical Engineering (Red X) is the technical problem solving strategy General Motors is using todrive Customer Enthusiasm in our products. The technology, pioneered by Dorian Shainin nearly 60 years ago, links engineering sciences, statistics and logic to solve technical problems with a high level of statistical confidence. A Red X project starts with a problem definition and ends with confidence that the problem was fixed. Since 1995, over one thousand Red X projects have been completed.
The General Motors Red X Program encompasses the Right People, on the Right Projects, utilizing the Right Strategy, to respond quickly to quality concerns of our customers.
The process compares the best and the worst vehicles and begins with answering important questions such as are the best people practices taking place and are the production assembly documents being followed.
If the answer to each question is yes, a clear problem definition is then determined. The steps to solving a problem not only answer, but also confirms that the answer is right. Red X members must prove that you can turn the problem on and off to confirm the answer is correct.
谢宁DOEShaininSystem
DorianShainin道林•谢宁1914-2000美国质量协会ASQ十八位荣誉会员之一,唯一获得ASQ美国质量协会颁发的四大奖。闻名于世是谢宁系统ShaininSystem或统计工程StatisticalEngineering。
2004年ASQ美国质量协会设立道林•谢宁奖。
1936年谢宁从麻省理工学院航空工程系毕业后,进入联合飞机公司(今联合技术公司)担任工程师,十六年后,他进入RathandStrong管理咨询公司,担任咨询师。1975年,成立谢宁咨询公司。
谢宁系统主要七种工具
多变差图Multi-variChart
部件搜索ComponentSearch
成对比较PairedComparisons
变量搜索VariableSearch
两水平全因子设计Full2nfactorial
红X的确认方法BvsC,
确定公差ScatterplotRealistictolerances
谢宁系统主要特点
由果寻因,基于事实结果反向搜索根本原因。
用系统的工具和渐进的过程搜索根本原因。
关键少数原理-根本原因RedX变差大于任何其他原因。
杠杆作用,采用极端的小样本搜索根本原因。
独特的Progressivesearch和条件交换方案,用较少的实验次数消除交互作用影响。
从SPC、DOE、数理统计和部件交换技术导出,用现成公式,而不需数理统计知识和计算。
整体方法是强大,某些的具体分析方法弱。
工具名称作为商标,很少文章讨论,公众不知详细内容。
SHAININDOE方法
古典和田口实验的替代品设计是鲜为人知但更简单的ShaininDOE方法由Dorian开发和完善Shainin(Bhote和Bhote,2000年),顾问和顾问在美国和欧洲超过750家公司。谢宁哲学一直是,“不要让工程师这样做猜测;让部分说话。“Shainin认识到了经验数据在解决现实世界中的价值问题。他介绍了红X的概念,占主导地位变异的来源,在众多来源中一个问题的变化,不可避免地占了几乎所有不必要的影响。事实上,Shainin(Shainin,1995;1993b),分类所有慢性质量问题的原因分为三个X,即红色X,粉色X-第二个最重要的原因,和淡粉色X-第三最重要的原因。
据他说,这三个Xs一起占变异的80%以上在规范限制内以及何时允许捕获,减少和控制,这些可以消除这种变化。
Shainin开发了技术(Shainin和Shainin,1990;1992年a;1992年b;1993年a;1993年b;谢宁,Shainin和Nelson,1997)追踪占主导地位通过消除过程来源(Shainin,1993b),称为渐进式搜索。这些技术也被提及作为
Shainin系统进行质量改进,开发出来在超过40年的时间里,很简单,但在同时功能强大且易于理解和实施在工业环境中。
在某种程度上,这些可以认为是非参数的等价物Taguchi的DOE因为他们没有做出任何限制性的假设关于人口参数。“百分之九十的公差和规格是任意决定,并不符合预期应用程序。这当然在很大程度上促成了许多东西被称为“慢性质量问题”-存在的问题重复。然后找到解决这些问题的方法对工程师和质量从业者来说是一项重大挑战。Shainin技术主要是已知的在消除方面取得突破性进展慢性质量问题。这些都非常有效确定根本原因并验证它。
古典和田口方法在中国的应用各个领域都得到了广泛的研究。一些最近在这方面的贡献来自王和Ren(2007),Singh,Maheswari和Pandey(2007),见和Wong(2008),Abdo(2008),Rao,etal(2008),andAnawa等人(2008年)。相比之下,Shainin系统有没有经过广泛的审查,学术和非常在这一领域开展了有限的研究。Bhote(1990)将Shainin
技术与实验设计进行了比较和田口方法,在语境中电子行业的结论是Shainin技术更简单,更便宜,更统计比其他两个强大。
Logothetis(1990)也评估了与之相关的Shainin技术田口方法和统计过程控制方法。Bhote(1991)和Bhote和Bhote(2000)描述这些工具在他们的书中,但有很多批评关于他们的说法和所描述的工具。
虽然尼尔森(1991),摩尔(1993),以及最近,Zeigel(2001)批评Shainin系统没有事实根据斯坦纳等人(2008年)对其进行了夸大其词认为Shainin系统背后的一些想法真的很有用。Goodman和Wyld(2001)提供了一个涉及使用ShaininDOE的案例研究在工业运作中。
这项研究表明'Shainin方法非常实用且很容易在许多环境中执行,使其成为最多的可用的质量技术.Verma,etal(2004)用一种稍微不同的方法来比较方法。在他们的研究中,有三例田口实验从现有文献中挑选出来然后重新应用Shainin方法找出答案它是否优于其他DOE技术。Taguchi和Shainin技术之间的比较在托马斯提供航空航天环境和安东尼(2005年)。其他一些研究过的作者这些技术是Traver(1995),Ledolter和Swersey(1997),Does,RoesandTrip(1999),DeMast,etal(2000)和Steiner和MacKay(2005)。摩托罗拉是众多使用过的公司之一这些工具。
虽然摩托罗拉取得了惊人的成功六西格玛方法现在已成为历史,一个鲜为人知的事实是Shainin技术是关键驱动因素之一他们的成功。摩托罗拉开始使用它们1980年取得了显着成绩。据Bhote说(1991),他做了大量的研究在这些技术中,“摩托罗拉的工厂,供应商和全球各地的客户进行了数百次作为六西格玛质量的一部分,Shainin实验“戴姆勒克莱斯勒,通用汽车,和德尔福公司是其他一些公司据报道,他们成功地使用了ShaininMethodology。美国质量协会(ASQ)非常最近设立了DorianShainin奖章以表彰他对发展Shainin的贡献现在被广泛认为是简单的技术,强大而实用的工具,帮助解决制造商的问题问题。2005年,统计学家卡尔班纳特是他在这一领域的工作是该奖项的第一个获奖者。经典DOE,TaguchiDOE和ShaininDOE是表2中相互比较。对这三种方法的研究清楚地表明了这一点Shainin工具比其他两个工具更具优势在成本,时间,培训,复杂性方面,范围和易于实施。