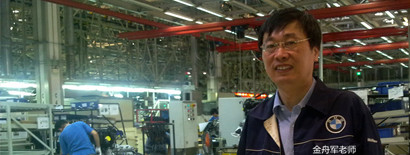
上海咨询公司PFMEA 过程潜在失效模式及后果分析培训公开课咨询课—欢迎企业内部培训和培训机构合作垂询
PFMEA 培训公开课-培训地点:江苏无锡万达广场 每月开班 小班教学、满四人开班
金舟军老师 手机/微信:13816949004 QQ邮箱:923503608@qq.com
以应用为导向的PFMEA培训咨询,学员培训后就会应用PFMEA,金舟军老师通过严格的培训流程确保顾客满意
请点击查看—金舟军质量管理工具培训咨询实施流程
PFMEA培训主讲质量专家金舟军,PFMEA培训机构上海科租企业管理咨询有限公司主办是专业、实战、解决问题的培训,PFMEA培训咨询包括FMEA实战案例及步骤、过程流程图、控制计划、作业指导书,PFMEA培训班和企业内训请垂询
请点击查看—金舟军质量管理工具培训咨询实施流程
PFMEA培训主讲质量专家金舟军,PFMEA培训机构上海科租企业管理咨询有限公司主办是专业、实战、解决问题的培训,PFMEA培训咨询包括FMEA实战案例及步骤、过程流程图、控制计划、作业指导书,PFMEA培训班和企业内训请垂询
最有价值的PFMEA培训公司
上海科租企业管理咨询有限公司金舟军老师自办过程FMEA培训咨询公司,培训老师自办公司省出了业务费用和老板利润,客户的培训费全部变为培训老师的培训费,能为客户提供优质服务,客户培训价值最大化值 。只要学员参加过质量培训课程,将为学员提供终生的培训课程答疑。
最具专业的PFMEA培训讲师
金舟军二十多年专业从事过程FMEA培训讲师,专业涉及质量管理和精益生产课程,客户涉及世界五百强企业, 每个培训项目的客户都有培训现场的视频和照片为证。金舟军老师课程以应用为导向,课堂上只讲干货,绝不以无关的游戏打发时间。
培训的客户-全部有客户培训现场照片、视频为证!

重庆长安汽车、上海延锋韦世通、上海NEC、上海德尔福、武汉东风汽车、江苏东风起亚、江苏麦格纳、安徽康佳电器、、安徽博西华、上海奥托立夫、浙江海信惠尔浦、沈阳宝马汽车、上海大金空调、辽宁大连固特异轮胎、长春大众集团、湖北武汉佛吉亚、上汽集团、吉林一汽集团、广西上汽通用五菱、广西玉林重工、江西长力股份 北京北汽福田、深圳中兴通迅、福建新能源科技、湖南三一重工、苏州恩斯克轴承、河北天威光伏、武汉哈金森、苏州力特奥维斯、重庆 嘉陵集团 福建奔驰汽车、辽宁大连大众变速箱 广东广州京信通信、深圳中兴通讯 河南利达光电 河南新乡豫新 河北莱尼、山东莱尼 、山东胜地、陕西中航、湖南时代电气、天津中核
FMEA培训课程公开课视频--点击图片即观看好看视频金舟军老师好看视频主页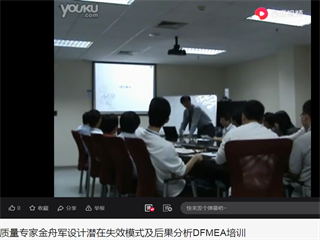

重庆长安汽车、上海延锋韦世通、上海NEC、上海德尔福、武汉东风汽车、江苏东风起亚、江苏麦格纳、安徽康佳电器、、安徽博西华、上海奥托立夫、浙江海信惠尔浦、沈阳宝马汽车、上海大金空调、辽宁大连固特异轮胎、长春大众集团、湖北武汉佛吉亚、上汽集团、吉林一汽集团、广西上汽通用五菱、广西玉林重工、江西长力股份 北京北汽福田、深圳中兴通迅、福建新能源科技、湖南三一重工、苏州恩斯克轴承、河北天威光伏、武汉哈金森、苏州力特奥维斯、重庆 嘉陵集团 福建奔驰汽车、辽宁大连大众变速箱 广东广州京信通信、深圳中兴通讯 河南利达光电 河南新乡豫新 河北莱尼、山东莱尼 、山东胜地、陕西中航、湖南时代电气、天津中核
FMEA培训课程公开课视频--点击图片即观看好看视频金舟军老师好看视频主页
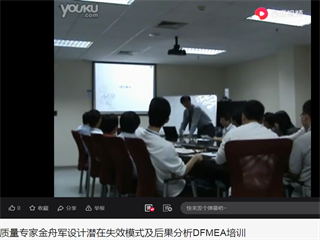
FMEA培训课程公开课照片
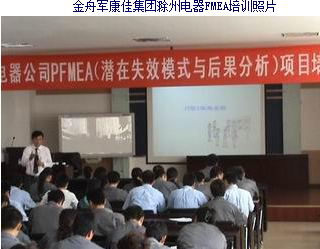
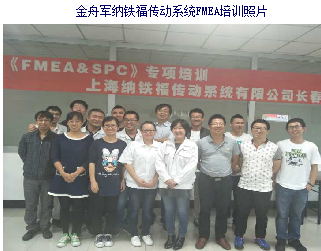
结合客户案例的实战型培训 包括后服务答疑的全过程
金舟军老师通过五大步骤结合客户案例讲解,确保学员学完全就会在工作中应用: 1 .案例网络调研、2.案例学员预习、3. 现场案例调研、4.案例练习点评、5.售后案例答疑。
1.案例网络调研
培训意向一经确定,金舟军老师就要与客户进行网络沟通,确定过程FMEA实施难点,收集过程FMEA实施资料,并就实施资料的细节进行沟通,并了解客户学习过程FMEA的目的。
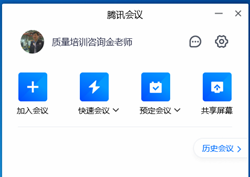
2.学员案例预习
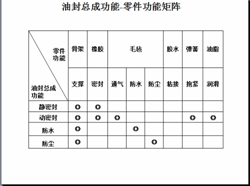
3. 现场案例调研
金舟军老师根据过程FMEA实施中的难点,事先为学员出过程FMEA的预习题,帮助学员提前思考怎样解决实施案例的难点,同时也预习课堂讲解的知识。
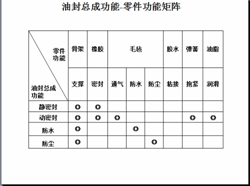
3. 现场案例调研
培训前一天,金舟军老师会到客户现场进行一天的现场调研,查找客户过程FMEA实施V情况,并为课堂针对客户实施过程FMEA中的问题讲解做准备。
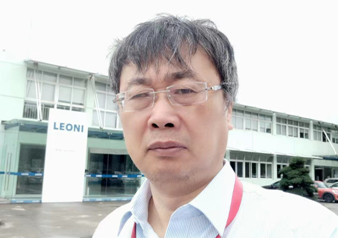
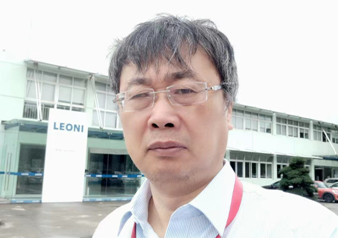
4.案例练习点评
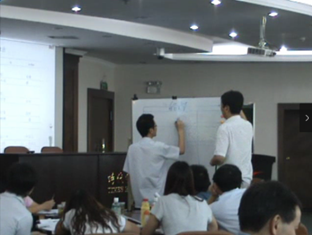
5.售后案例答疑
培训完成后一年之内,如果客户在实施过程FMEA过程中有什么问题,可以为客户组织腾讯会议的在线答疑至少三次。
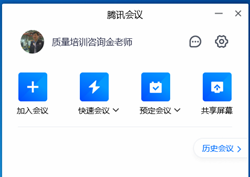
根据案例实施中的难点问题,每天培训约有五十分钟的客户案例分组练习,每组学员的案例练习金舟军老师都要做详细的点评,确保学员学完全就会在工作中应用。
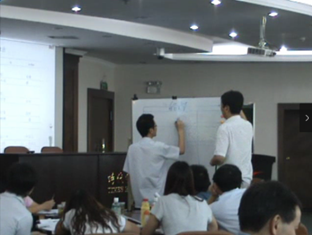
5.售后案例答疑
培训完成后一年之内,如果客户在实施过程FMEA过程中有什么问题,可以为客户组织腾讯会议的在线答疑至少三次。
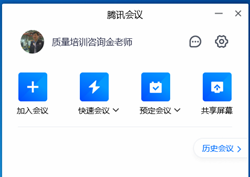
根据案例实施中的难点问题,每天培训约有五十分钟的客户案例分组练习,每组学员的案例练习金舟军老师都要做详细的点评,确保学员学完全就会在工作中应用。
培训课程公开课大纲
一. 过程FMEA培训目的:通过本课程的学习, 使学员能熟练运用PFMEA分析和评价本岗位或本工序潜在失效模式及后果
分析,并能制定相应错误预防措施,以使所有过程的作业指导书源于该过程的PFMEA。
二. 过程FMEA培训对象:采购、仓贮、设计、工艺、设备、工装、计量、检验、营销、培训等所有过程的人员。
三. 过程FMEA课程内容
1.过程设计和开发 金舟军原创 抄袭必告
过程三次设计
工艺设计-工艺路线方案设计
工艺参数设计-用实验设计确定工艺参数最佳组合
公差设计-结合生产精度,确定工艺参数-允许范围
案例讨论-产品设计和开发与过程设计和开发的主要金区别是什么
2. 产品制造和装配的控制
产品设计和开发VS产品制造和装配
过程方法
过程的要素及特点
过程的监视测量
过程特性&产品特性
产品特性-过程特性因果矩阵
关键产品特性KPC-关键过程特性KCC
案例讨论-完成你所熟悉过程的产品特性-过程特性因果矩阵
3.过程控制
探测控制措施 金舟军原创 抄袭必告
产品检验
预防控制措施
过程控制系统
案例讨论-产品设计和开发与过程设计和开发的主要舟区别是什么
4.PFMEA简介
制造过程的问题
PFMEA目的
PFMEA思维过程系统化 规范化 文件化
FMEA的发展历史
FMEAs的种类 Automotive
FMEAs 关联
内容和时机
动态的PFMEA
PFMEA与APQP关系
案例讨论- PFMEA是怎样防止很多召回事件的发生
5.PFMEA分析五大要素
过程功能
产品功能VS过程功能
产品功能VS产品特性
过程功能&过程特性的层次关系
过程潜在失效模式
失效的潜在起因VS过程潜在失效模式
潜在失效模式识别方法 金舟军原创 抄袭必告
预期潜在失效模式-非预期潜在失效模式
过程潜在失效后果
顾客功能-技术功能矩阵
四个主要顾客失效模式后果
过程潜在失效后果识别方法
失效的潜在起因/机理
根本起因五个方面
根本起因两个阶段
现行过程控制
工艺验证和SOP等控制方法
预防维护vs预测性维护
作业准备验证
标准作业
判断检验
信息检验
溯源检验
案例演练-完成你所熟悉过程的PFMEA
6.PFMEA项目舟实施流程十五步骤
PFMEA项目的管理 关键日期的控制
组成PFMEA小组
产品设计输出&顾客要求
产品特殊特性识别
产品和部件生产流程图
过程识别
产品特性-过程特性矩阵
编制部件过程流程图
PFMEA小组任务分配 金舟军原创 抄袭必告
进行PFMEA分析
跟踪措施
过程流程图、控制计划、作业指导书与PFMEA的关联
PFMEA更新
持续改进、8D中PFMEA的评审更新 与PFMEA相关文件的更新
7. FMEA填表&RPN值评估
严重度 S 表Cr1推荐的PFMEA严重度的评价准则
频度 O 表Cr2PFMEA频度建议评价准则
探测度D Cr3推荐的PFMEA探测度评价准则
确定措施优先顺序
风险评估;风险顺序数(RPN)
RPN限值法
确定优先措施
案例演练-完成你所熟悉过程的PFMEARPN值评估
8.五大过程PFMEA的详解
加工程PFMEA详解
检验PFMEA详解
贮存PFMEA详解
搬运PFMEA详解
采购过程PFMEA详解
案例演练-完成你所熟悉五大过程PFMEA
9.FORD machinery FMEA简介 金舟军原创 抄袭必告
10.最新版AIAG-VDA FMEA七步法
定义范围
结构分析
功能分析
失效分析
风险评估
优化
结果文件化
结果文件化
11.最新版AIAG-VDA FMEA的SOD评分的军变化
RPN的评论
AP行动优先级评估方法
12.最新版AIAG-VDA FMEA的FMEA表格的变化
结构分析
功能分析
失效的后果-失效模式-失效起因
13.FMEA软件与FMEA资料库建立(有FMEA软件光盘提供)
IQ-RM软件FMEA应用介绍
四. 过程FMEA培训课程学时: 每天6.5小时 共两天14小时
PFMEA培训机构上海科租企业管理咨询有限公司
过程FMEA简介
过程FMEA是由负责制造/装配的工程师/小组主要采用的一种
分析技术,用以最大限度地保证各种潜在的失效模式及其相关
的起因/机理已得到充分的考虑和论述。FMEA以最严密的方式总结了开发一个过程时小组的思想。(其中包括根据以
往的经验可能会出错的一些项目的分析)。这种系统化的方法体现了一个工程师在任何制造策划过程中正常经历的
思维过程,并使之规范化。
过程FMEA:
确定过程功能和要求;
确定与产品和过程相关的潜在的失效模式;
评价潜在失效对顾客产生的后果;
确定潜在制造或装配过程起因并确定要采取控制来降低失
效产生频度或失效条件探测度的过程变量;
确定过程变量以此聚焦于过程控制;
编制一个潜在失效模式的分级表,以便建立一个考虑预防/
纠正措施的优选体系;
记录制造或装配过程的结果。
顾客的定义 过程FMEA中“顾客”的定义通常是指“最终使用者”。然而,
顾客也可以的随后或下游的制造或装配工序,维修工序或政府法规。
小组的努力 在最初的过程FMEA过程中,希望负责的工程师能够直接地、
主动地联系所有有关领域的代表。这些领域包括(但不限于)
设计、装配、制造、材料、质量、服务和供方,以及负责下一层次装配的领域。过程FMEA应成为促进各相关领域之间
相互交换意见的一种催化剂,从而推进小组协作的工作方式。
除非负责的工程师有FMEA和团队工作推进经验,否则,有一位有经验的FMEA推进员来协助小组的工作是非常有益的。